Case History
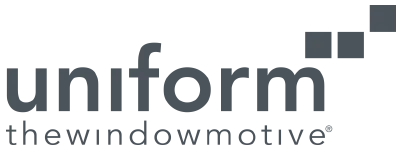
Via dell'Agricoltura 36
37046 Minerbe (VR) - Italy
www.uniform.it
uniform@uniform.it
Tel +39 0442 669669
Uniform Spa
Furniture Complements & Construction
Uniform Spa was founded in 1988 with the aim of making Italy's first wood-aluminum and wood bronze window and door system.
Today Uniform, designs, develops and manufactures wood-aluminum window and door systems, with its headquarters in the province of Verona. Technology, Trend and Solutions are the identity to best serve the customers who are mainly window manufacturers.
The mission is to offer high quality sustainable systems to expand the market of window and door interpreters, improve window and door productivity and customer welfare.
The daily work is made up of about 1,200 customers, 20,000 sales orders, 700,000 production orders.
Logistics Experience
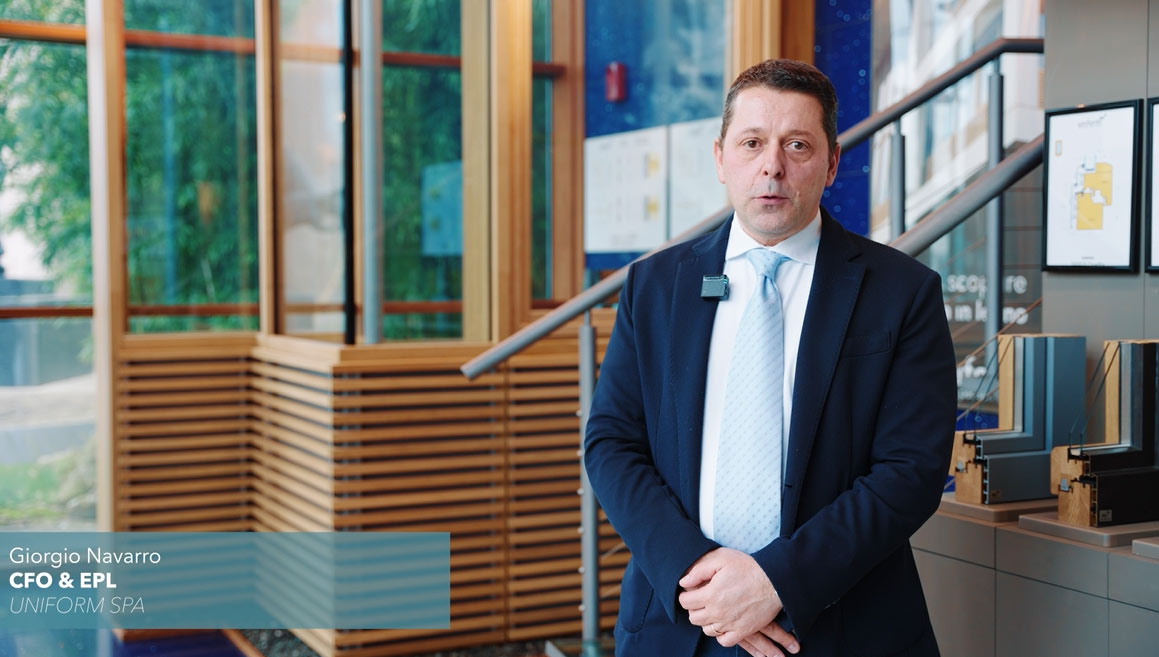
Logistics Experience - Uniform Spa
Interview with Giorgio Navarro - CFO & EPL Uniform Spa
The flow analysis and software implementation phases were the result of excellent collaboration between Uniform and Replica Sistemi staff.
Giorgio Navarro
CFO & EPL Uniform Spa
Uniform
Uniform in numbers
CUSTOMERS
SALES NUMBERS
PRODUCTION NUMBERS
Needs and Project
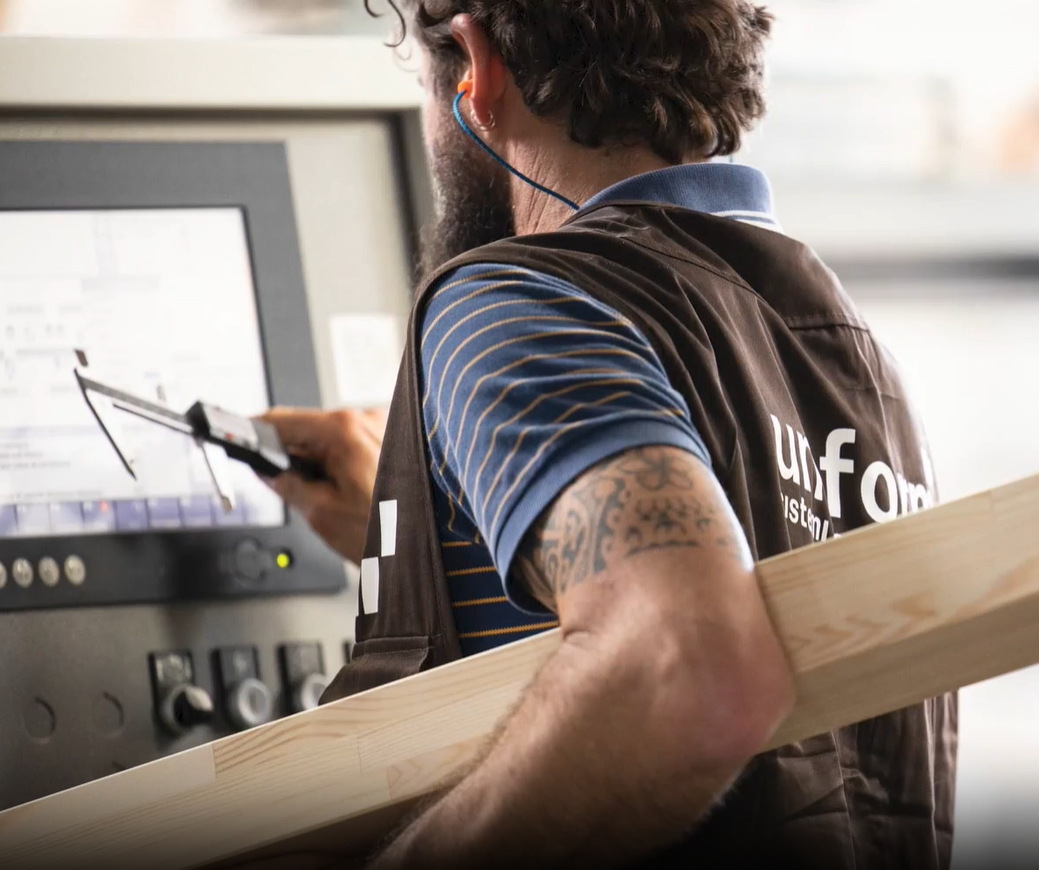
Needs
Uniform's production is primarily order-based, with orders being fulfilled based on the bill of materials for each order.
A section of the warehouse is allocated for the storage of components and spare parts for customers.
The materials stocked are of various types, sizes, weights and volumes, including, but not limited to, paint powders, wooden boards, handles, hinges, window covers, and screws.
When receiving all these items from suppliers, there was no immediate coding system to upload the stock to the ERP.
The result was that the purchasing process was based on estimates of actual business needs, rather than the more accurate real-time data that a coding system would provide. This sometimes led to shortages on the production line, resulting in production stoppages.
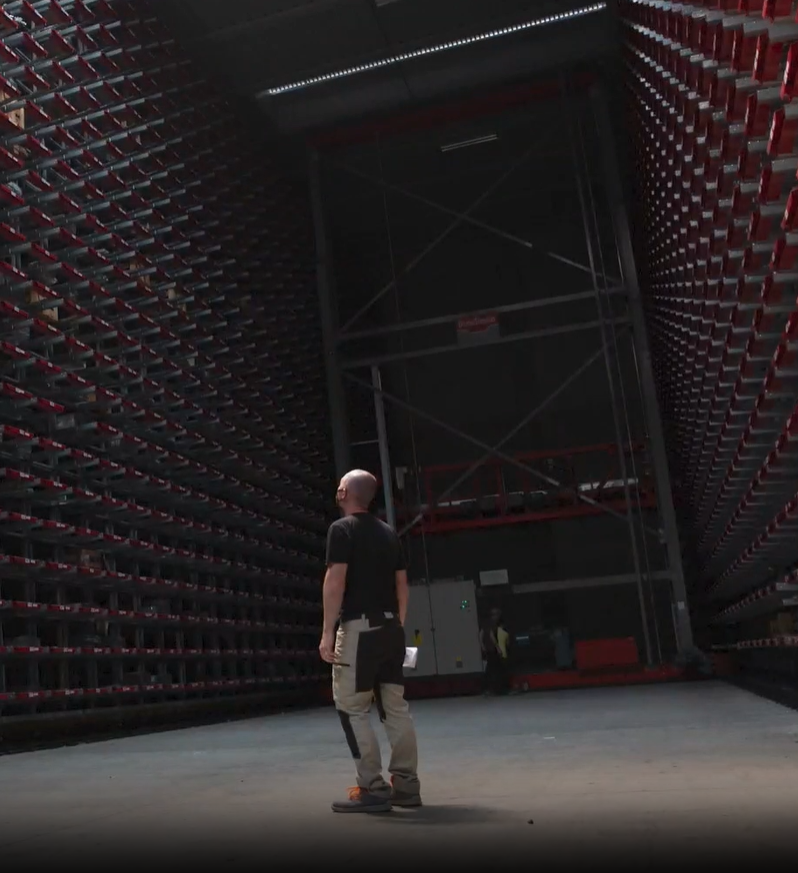
Project
Following the implementation of the Replica Infinity WMS, a labelling system was activated for all incoming materials. This system allows the identification, registration and tracking of raw materials and components with precise stock data for each item captured by the WMS and recorded on the ERP.
In accordance with the production bill of materials, materials are called up on the line and, thanks to the interface with the ERP, components are immediately unloaded in the warehouse for real-time inventory.
Once the production process has been completed, the WMS takes charge of the windows and doors produced. The WMS identifies the warehouse spaces where they are allocated, speeding up and making precise the process of preparing the order to be sent to customers.
The benefits of integration
Uniform is now a prime example of a digital supply chain, with OperaMES and Zucchetti's WMS Replica playing a key role in digitising and optimising the process from production to logistics.
Future steps
Download case history in .pdf