Case History
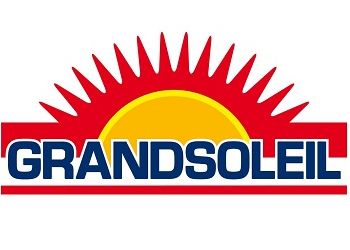
Via Garibaldi, 244, 46013 - Canneto sull'Oglio - MN
Tel: +39 0375 7172200
Igap Spa
Furniture Complements & Construction
Igap Group produces and sells articles for camping, gardening and leisure and supplies most of the European retail and large distribution network.
Igap currently works with a facility of around 120,000 sqm, including 75,000 sqm of covered surface, and with an on-going project of building new warehouses for 18,000 sqm, thanks to which the company can grant extremely rapid delivery times for at least 95% of received orders.
Logistics Experience
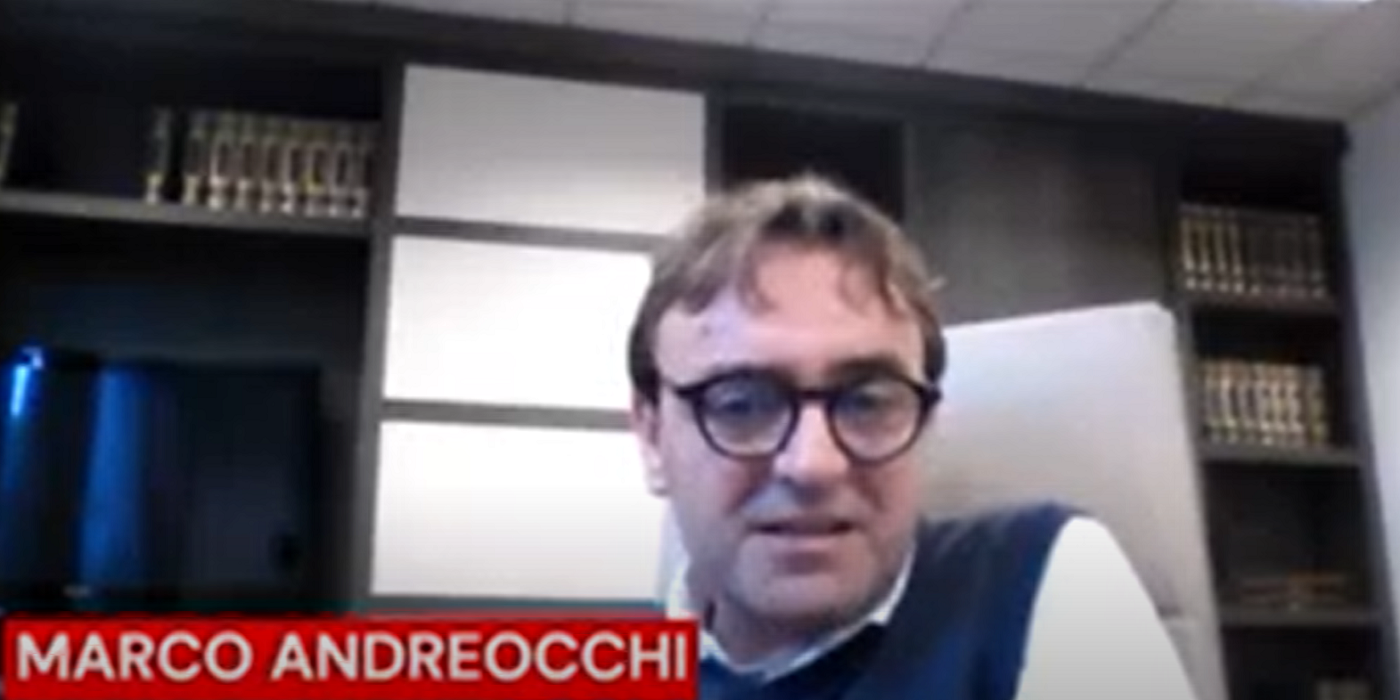
Logistics Experience - Igap Spa
Interview with Marco Andreocchi
NUMBERS
The numbers of Igap Spa
ACTIVE CLIENTS
YEARLY SALES
REFERENCES
MILLIONS KG PLASTIC MOVED YEARLY
SQM PRODUCTION PLANT
SQM COVERED SURFACE
Project Goals
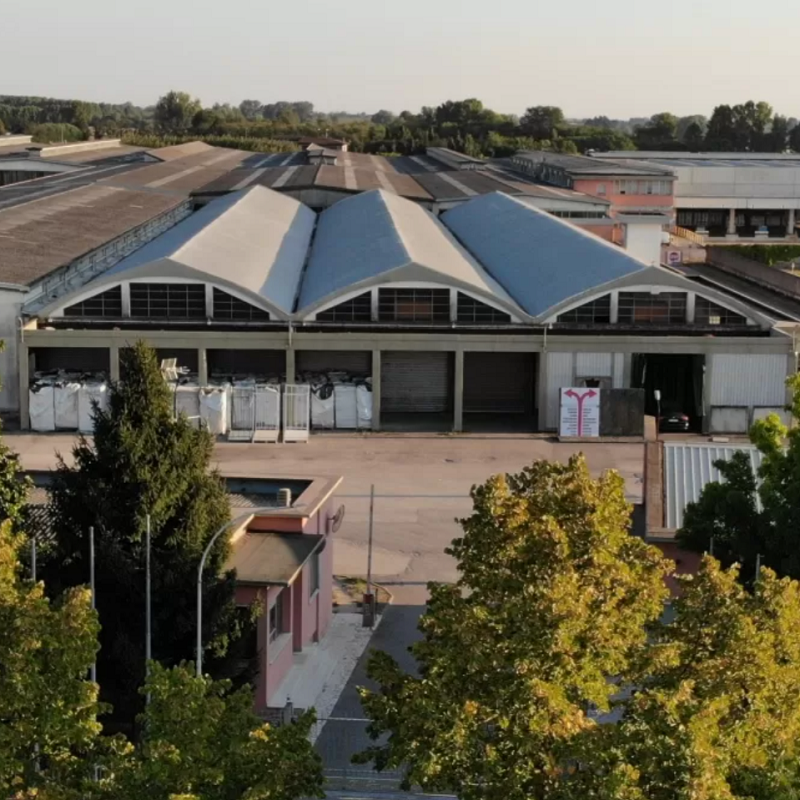
COMPANY STRUCTURE
Igap is a company with more than 60 years of experience in trading garden and indoor furniture.
Since 2005 it has also been in charge of production, which has been managed internally since 2014. The entire production process takes place at the plant in Canneto sull`Oglio (MN), starting with the raw material, the plastic granule, which is combined according to precise recipes to create the "mixture" from which the semi-finished products are made, and ending with the finished products.
The business is characterized by a strong seasonality: up to 150 employees are employed between fall and spring to cope with peak production, twice as many as in the summer period, when product distribution is concentrated throughout Europe and overseas-particularly to French supermarkets (58% of sales).
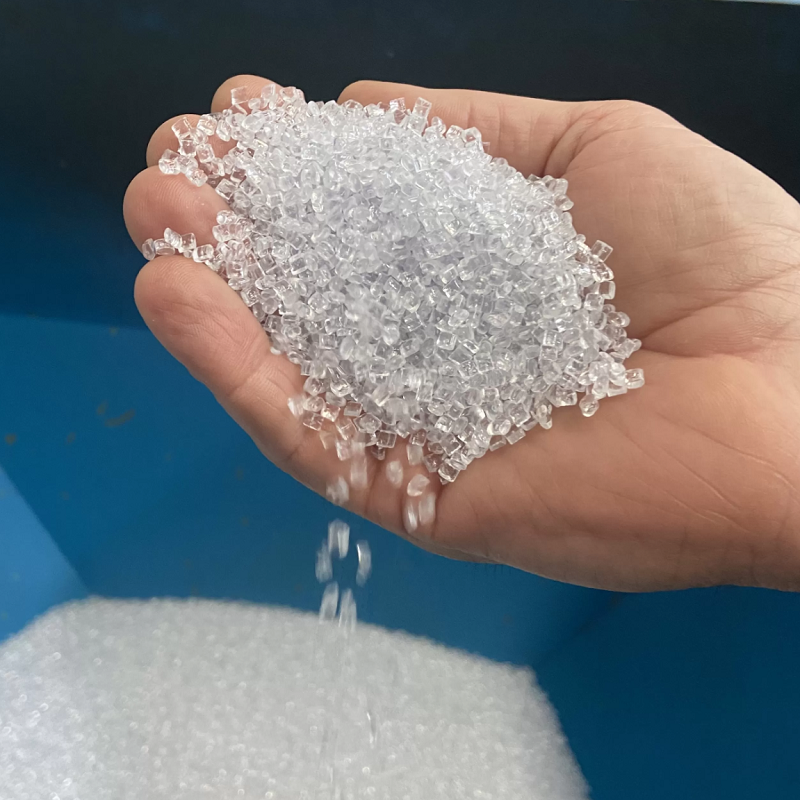
LOGISTICS NEEDS
Once production activities were implemented, the need arose to optimize their management through a business digitization process.
Production and warehousing operations were managed manually, causing errors in the recording of products: incorrect or missing inventories, stock shortages, and waste of time and resources in "chasing data."
Igap's main goals were:
- production planning;
- control of flows in the warehouse, from raw material to shipment to the customer;
- automatic recording of produced goods.
The Project
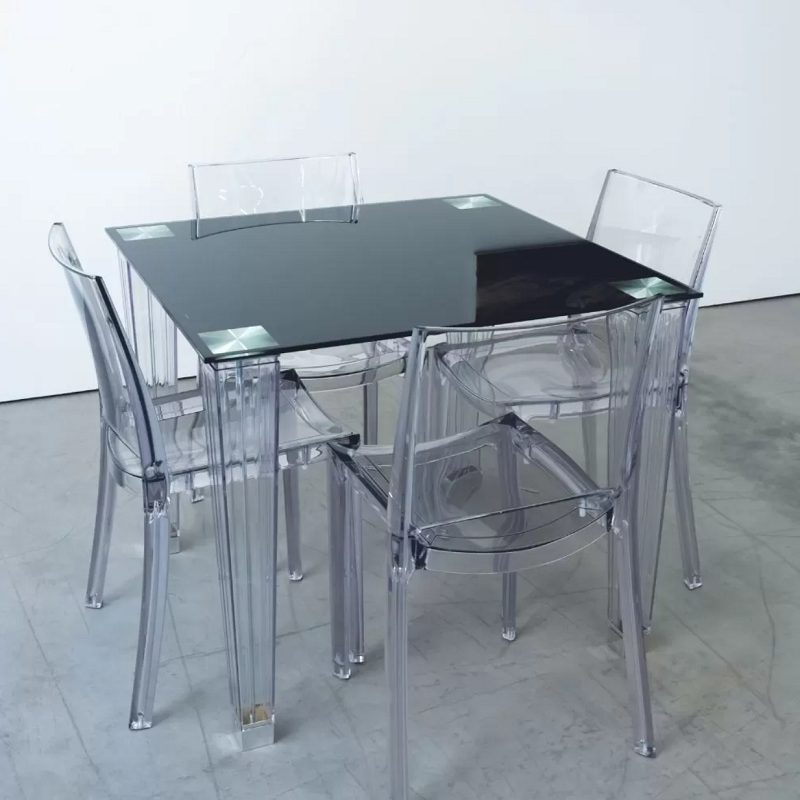
STOCKSYSTEM
The collaboration between IGAP and Replica Sistemi began in 2006 with the implementation of the StockSystem WMS.
The WMS manages and records all warehouse activities, guaranteeing complete real-time traceability from the arrival of the raw material to the shipment of the order.
The resource savings achieved through StockSystem also enabled the company to introduce a new quality control department, which is also interfaced with StockSystem.
For the operators, previously in charge of production inventory control, this also means dedicating their work to higher value-added activities.
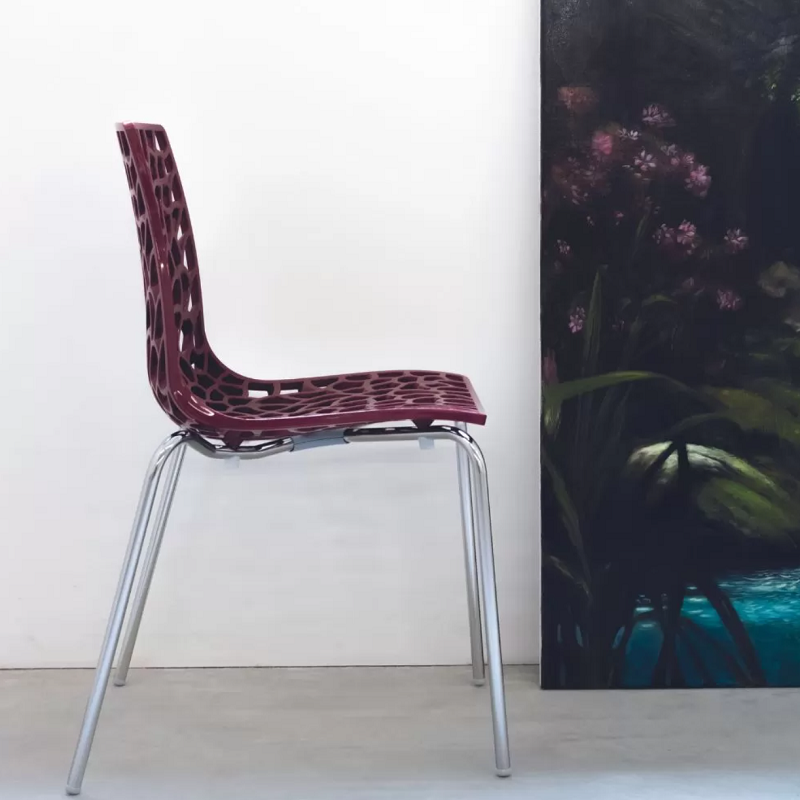
DYNAMICS NAV
In 2019, the Microsoft Dynamics Nav ERP implementation project began.
"When we found out that Replica had started covering Nav, which we were interested in, the choice was obvious. Integrating the WMS with the ERP was easy; we were just patched together."
- Marco Andreocchi, Production Manager Igap Spa
The software has been active since 2020 with no interruption. It is integrated with both StockSystem and the company's MES and communicates production orders to the machines.
"It's an articulated project focused on production, which is the heart of this company. The goal is to keep evolving the product on various areas."
- Simone Manfredini, Project Manager Replica Sistemi
The Results
The use of the StockSystem WMS has led to a drastic reduction in errors in production and distribution, consequently avoiding stock breaks, production interruptions and costly international returns.
Stocks are automatically recorded and immediately verifiable.
An additional advantage of the WMS is the rapid training of new operators, who can now start working independently after 2-3 days of induction into the warehouse.
The Dynamics Nav ERP has enabled the integration of all company departments for smooth and direct management of workflows, especially improving production control.
Next Steps
Igap is currently planning to move to the web version of the ERP, Microsoft 365 business Central.
Other plans for future developments include:
- greater integration of the company`s MES into NAV software;
- production cost budgeting and management;
- deeper integration of the manufacturing plant with factory systems to achieve more accurate analysis.
Download the .pdf file